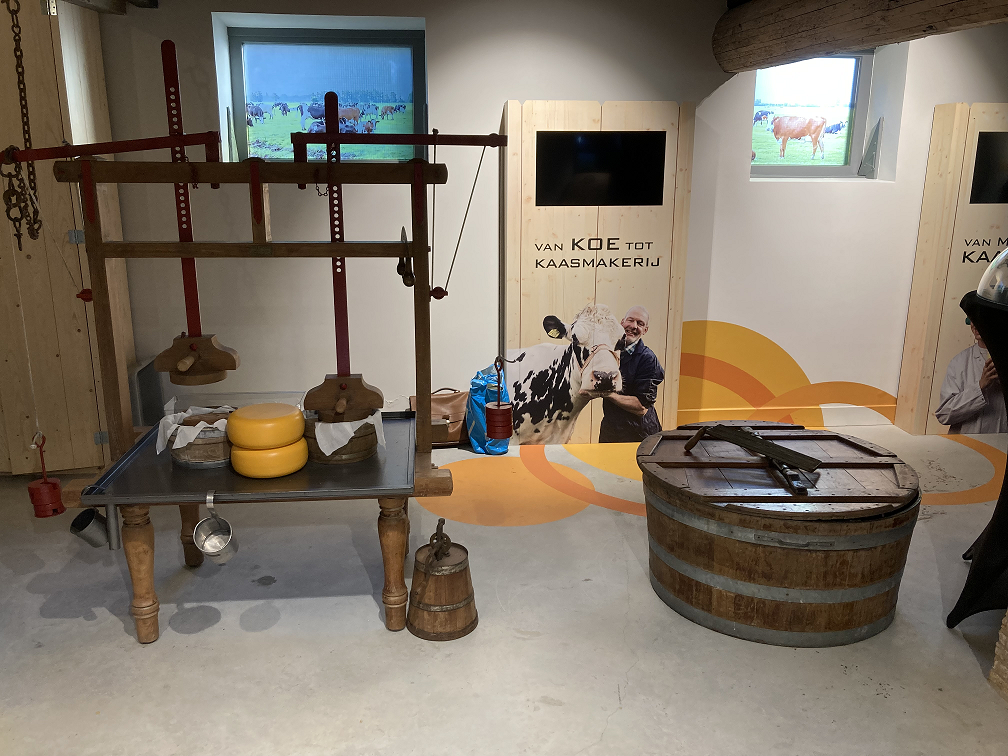
News
LMS allows De Graafstroom to opt for more cost-efficient MES alternative
- 25 March 2024
'Lean' MES
A standard MES offers a lot of functionality to monitor, control production processes and exchange information with ERP systems. The disadvantage is that you pay high recurring license fees if you only use a small part of these functionalities.
That was the dilemma for dairy De Graafstroom when the 8-year-old MES solution for the control of the warehouse could no longer be upgraded and supported. ICT Group has been working for De Graafstroom for years and came up with a more cost-efficient alternative: a Line Management System without license costs, but with customer-specific functionalities. A 'lean' MES solution that has been developed for use by multiple customers.
.NET webportal
Frank Baars, project & operations manager at ICT Industry & Infra: "Their current MES application takes care of the handling of the cheeses in their warehouse, from brine bath to truck. This involves all kinds of customer-specific requirements for automatic data exchange between ERP, PLC, weighing/labelling system and material movements. After analyzing all the functionalities, we quickly came to the conclusion that there is no standard MES that offers that. Even if we did opt for a standard MES, we had to add functionalities within the application."
Flexible MES solution
“During the quotation process, a solution was developed which is made up of the techniques with a .NET application with a Web portal, where the knowledge is widely available within ICT. Then you have flexibility without high annual license fees. A possibility for MES solutions that should not be too expensive, but do require customer-specific functionalities. De Graafstroom has chosen this solution because both the initial and annual investments are lower than those of a standard MES product solution. An MES solution that our engineers have already implemented at other clients and that ICT Group's Managed Services supports, manages and maintains. At De Graafstroom, we also have an SLA for management and maintenance and to fix malfunctions."
"ICT Group has provided us with a hassle-free replacement of the MES."
Pieter Franke, Head of Warehouse at De Graafstroom
Rotate Shadow
"For the construction of the LMS, ICT Group described all the functionalities. In addition, ICT Group planned and carried out the work for the Graafstroom. In consultation, we have chosen to first let the new LMS application run shadow next to the outdated MES. Especially the built-in functionalities demanded attention. You only see in practice how they manifest themselves. This allowed us to monitor data, check signals, compare anomalies and test and implement optimizations without downtime and loss of production. A very powerful testing method. With the 'go live', it turned out that only minor adjustments were needed, which we quickly implemented."
Broad applications of Lean MES
This concept lends itself perfectly to smaller and medium-sized production sites where a standard MES is too expensive and too bulky. Think of the food industry, chemicals. An LMS solution with at least the same functionality is cheaper to build and to maintain and manage by Managed Services. The in-depth technological expertise and domain knowledge of ICT Group's software developers and engineers offer customers solutions in this field to support their business-critical processes and strengthen their market position.
About De Graafstroom
Since 1908, Bleskensgraaf in South Holland has been home to the De Graafstroom dairy factory. A dairy factory 'for farmers, by farmers' where honest milk is made into an honest end product: cheese from the heart. "And we do that with pleasure, day in, day out." De Graafstroom has been owned by dairy cooperative DeltaMilk since 2009. Some 190 affiliated dairy farmers now own the factory, which annually processes 450 million litres of milk into 45,000 tonnes of naturally ripened round and rectangular Gouda cheeses.